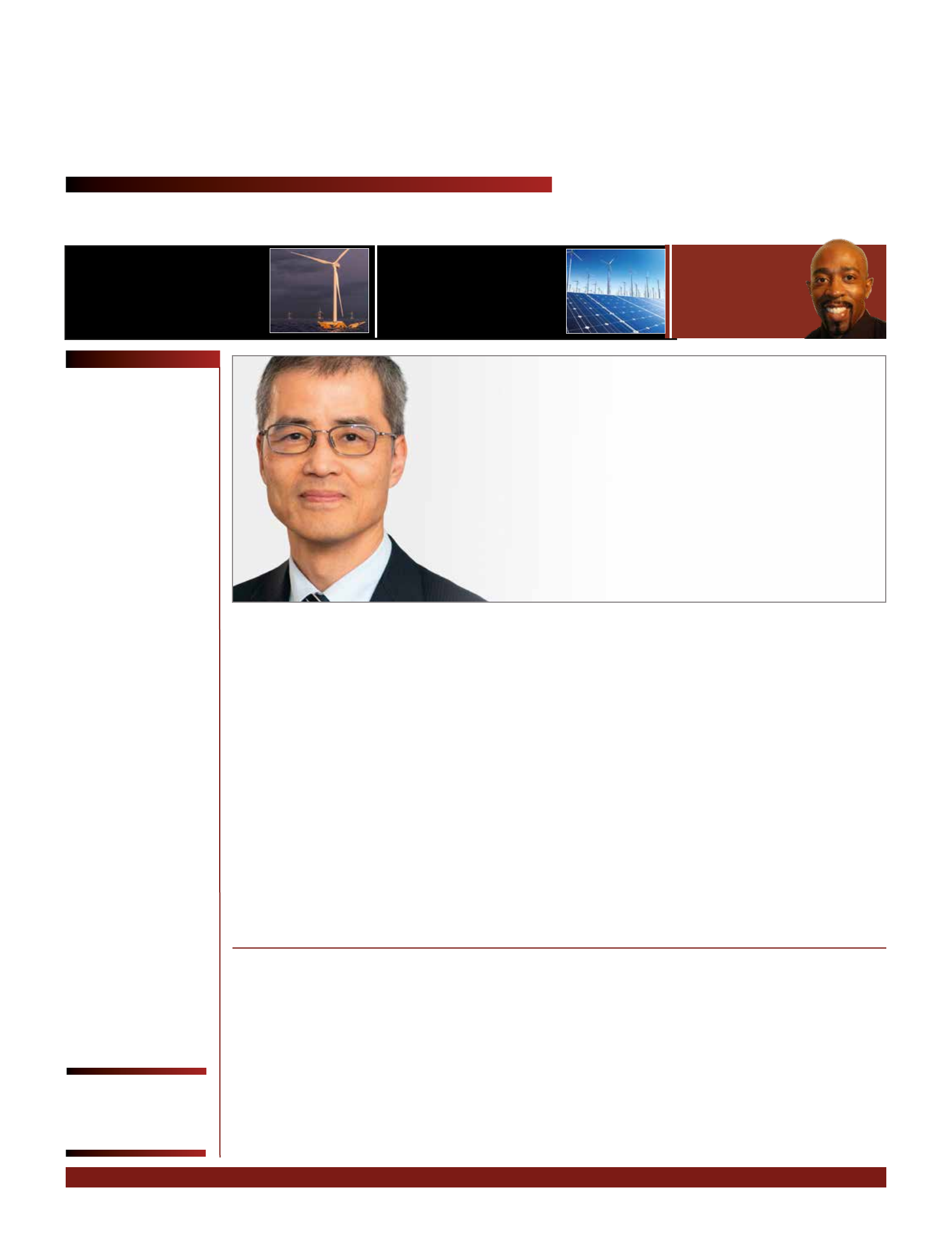
I
t’s well known that winds are
stronger and more consistent in
deep-sea waters compared to on-
shore or nearshore environments.
This makes offshore wind a vast, un-
tapped resource for clean energy that
humanity has hardly scratched the
surface of in trying to capture and
utilise. Part of the complication has
been getting massive wind turbines,
sometimes as tall as the Eiffel Tower,
out to sea cost-effectively. Getting
turbines onto xedbottom platforms
is already challenging enough, but
even more so when turbines are
placed on oating platforms and sub-
jected to the forces of the wind,
waves, tides, and currents.
Floating platform technology that
would support the largest turbines
(up to 15 MW) is part of a larger
puzzle that includes making sure that
wind farms can be developed at a
similar cost to offshore wind farms
with xedbottom foundations or
even onshore wind farms. Conserva-
tive potential market estimates proj-
ect over 00 GW of oating offshore
wind capacity by 2050, the amount
needed to reduce carbon emissions
levels and stay on track with the
agreed-upon 1.5°C above pre-indus-
trial global surface temperatures.
This would account for almost 15 per
cent of all projected offshore wind
production. However, oating off-
shore wind faces several obstacles
hindering its development, particu-
larly related to cost.
According to the National Renew-
able Energy Laboratory (NREL), the
Levelised Cost of Electricity (LCOE
– or the average cost of electricity
generation for a given generator over
its lifetime for a oating offshore
wind farm is estimated at $145/
MWh, signicantly higher than the
MWh for xedbottom offshore
wind farms. This cost disparity has
been the biggest barrier to oating
offshore wind projects achieving
widespread adoption and commercial
viability.
chieving the next phase of wind
power by deploying oating offshore
wind platforms farther into the sea
requires lowering the high initial
capital expenditures and operational
costs associated with its technology.
Developers must embrace innovation
in design and construction, strategic
nancial planning, and efcient op-
erational procedures and practices.
ome capital and operational ex-
penditures are out of oating wind
technology developers’ control, such
as interest rates and the costs of ma-
terials like steel, concrete, or copper.
Those materials are used in the sub-
structure and foundation, or oating
platform, which accounts for approx-
imately 30 per cent of the total
LCOE, according to NREL. There-
fore, technologists should look to use
fewer materials or enable mass man-
ufacturing of materials to deploy
platforms at lower costs.
Floating offshore wind platforms
offer a solution to harness wind pow-
er in ocean waters where xedbot-
tom foundations are impractical or
unfeasible, such as around island na-
tions. or example, Japan has ap-
proximately 0 000 m of coastline
and extremely deep coastal waters.
However, many oating platforms
today were developed for the oil and
gas industry or optimised based on
those legacy designs over a long pe-
riod of time. But innovation and new
approaches are desperately needed
for those optimised designs to evolve
and for the industry to achieve lower
costs.
Developers can look to the ship-
building industry to tackle this barri-
er. For centuries, shipbuilders have
been rening the optimal designs and
construction techniques based on the
materials and technologies available
to them in order to put massive oat-
ing structures out to sea. At the same
time, these shipbuilders have found
ways to manage operational and cap-
ital costs to keep them relatively low
despite the ships complexity and
size.
Drawing inspiration from this in-
dustry, where modular construction
has long been used to optimise costs
and efciency, oating wind farms
can be designed for rapid assembly
and reduced input material usage.
or example, a modular approach en-
ables local manufacturing, allowing
individual components to be fabricat-
ed at multiple locations near a partic-
ular wind farm site or port and trans-
ported to the installation site at sea
for assembly. This approach reduces
the need for large-scale, single-pur-
pose-built specialised fabrication fa-
cilities and minimises the inherent
logistical nightmare and excessive
costs of transporting large structures.
The focus must rst be on the sub-
structure – or platform – design and
construction.
The integration of advanced mate-
rials and engineering techniques can
further drive down costs. Advanced
materials, lie carbon bre compos-
ites, are lightweight yet supportive
and can reduce the overall weight of
the platform, thereby lowering mate-
rial costs and improving platform
stability. Adopting hybrid designs
that combine the best features of tra-
ditional oating platform designs has
shown promise in reducing steel us-
age by up to 70 per cent and cutting
mooring loads by 50 per cent, direct-
ly contributing to a lower LCOE.
Traditional oating platforms lie
semi-submersible, tension-leg, and
spar-buoy designs require substantial
quayside space, or the space around
the harbour’s platforms that project
into the water that is normally used
for loading and unloading boats.
They also need very deep waters for
assembly, turbine towers, and turbine
engines before they are deployed at
sea.
For a long time, the consensus was
that these two issues necessitated
costly port upgrades, adding yet an-
other expense to the overall oating
wind project and creating a signi-
cant nancial barrier to the sectors
growth. Minimising dependency on
specialised port infrastructure is an-
other focus area for lowering costs.
Modifying ports to accommodate
large oating wind platforms is an
additional high investment cost that
presents a signicant nancial barrier
to the sector’s growth.
As with the foundation and sub-
structure design and construction
strategy, at Gazelle Wind Power, we
have found that it is possible to work
within the constraints of many ports
as they exist today by rethining the
approach to platform design and as-
sembly with modular components
and local fabrication. Platforms with
lower drafts (the vertical distance be-
tween the waterline and the platform
base that do not require extensive
and expensive dredging could be im-
mensely impactful to achieving this
goal. The cost of dredging and deep-
ening ports is not just nancial it
also has extensive environmental im-
plications, with potential long-term
impacts that could lead to further de-
lays and additional costs.
Modularity in platform design
again becomes a viable option here
since they can be assembled on-site
using existing quayside space. nly
a minimal amount of port space
would be needed for nal assembly.
With the remaining space, operators
can assemble additional platforms
and turbines or continue port opera-
tions as normal. This approach is
similar to how shipbuilders use
oating docs to assemble large
sections of a ship before nal as-
sembly. Using these techniques,
oating wind projects can avoid
bottlenecks and high costs associat-
ed with specialised port renovations
and infrastructure.
Having the right digitilisation strat-
egy is essential to achieving bank-
ability and ensuring the long-term
success of the oating wind project.
According to the International En-
ergy Agency, global investment in
digital electricity infrastructure and
software has grown 20 per cent an-
nually since 2014. Digital tools like
predictive maintenance systems, re-
mote monitoring, and advanced ana-
lytics are transforming the operation-
al landscape for almost every
industry, especially for nextgenera-
tion renewable energy sources like
oating offshore wind. They allow
operators to detect potential issues
early, mae efcient maintenance
schedules and processes, and reduce
the downtime for turbines.
Digital technology is crucial for
oating offshore wind, which re-
quires constant monitoring due to
the inherent chaotic and unpredict-
able forces of nature associated with
the high seas. Monitoring systems
allow operators to track real-time
data on platform performance and
even meteorological and environ-
mental conditions. By predicting
potential failures before they hap-
pen, operators can lower the risk of
accidents and enhance the overall
safety of maintenance workers and
operational staff.
In addition to predictive mainte-
nance, having the right digital assets
enables optimised turbine position-
ing and allows operators and asset
managers to make remote adjust-
ments of ballasts or stabilisers, there-
by maximising energy output.
ne of the biggest nancial riss in
oating wind project development is
the time lag between a project’s pro-
posal and securing permits, licenses,
risk assessments, or signing a Power
Purchase Agreement (PPA). During
this lag period, uctuating economic
conditions lie ination, commodity
pricing, and interest rates can impact
the overall viability of a project.
Therefore, nancial models need
room for exibility to account for
these changing variables.
Clauses that allow for indexation or
adjustment of the price for ination
and market changes are crucial to in-
clude in any development agreement
or PPA to ensure projects can remain
protable even when costs change.
Securing long-term contracts for dif-
ference (CfDs), where a government
will provide the project with a vari-
able premium on top of the market
price, can provide reliable and pre-
dictable revenue streams, making
these projects more attractive to
lenders, partners, and investors.
Specialised insurance that covers
construction, operational, or even en-
vironmental risks can provide an ad-
ditional layer of security for inves-
tors and stakeholders. Allocating
risks among the vested parties, in-
cluding developers, contractors, and
insurance companies, further attracts
funding for development and deploy-
ment with the added benet of nan-
cial stability.
nsuring the success of the oating
offshore wind platforms, projects,
and the overall industry requires a
multi-faceted approach, and each
piece must mae sense and t seam-
lessly. By focusing on innovative de-
signs, leveraging scalable, modular
construction methods, reducing reli-
ance on expensive port upgrades and
renovations, embracing digital tools
for efciency, and mitigating nan-
cial riss through strategic nancial
structures, the industry can overcome
the cost hurdles and drive wide-
spread adoption. Just lie assembling
a puzzle, each component – techno-
logical, operational, and nancial
must come together perfectly to cre-
ate a sustainable and affordable
solution for oating offshore wind
deployment.
Alvaro Ortega is CFO of Gazelle
Wind Power, the developer of a next-
generation oating offshore wind
platform.
Offshore wind is
a vast, untapped
resource for clean
energy that humanity
has hardly scratched
the surface of in
trying to capture and
utilise. Part of the
complication has
been getting massive
wind turbines out to
sea cost-effectively.
Floating platform
technology that
would support the
largest turbines is
part of a larger puzzle
that includes making
sure that wind farms
can be developed
at a similar cost to
offshore wind farms
with xed-bottom
foundations. Gazelle
Wind Power’s
Alvaro Ortega
explains.
Facing the cost headwinds in
Facing the cost headwinds in
aisi
THE ENERGY INDUSTRY TIMES - OCTOBER 2024
13
Energy Outlook
Aississiai
Paa
aaai
asa
iaas
industry or optimised based
on those legacy designs over
aii