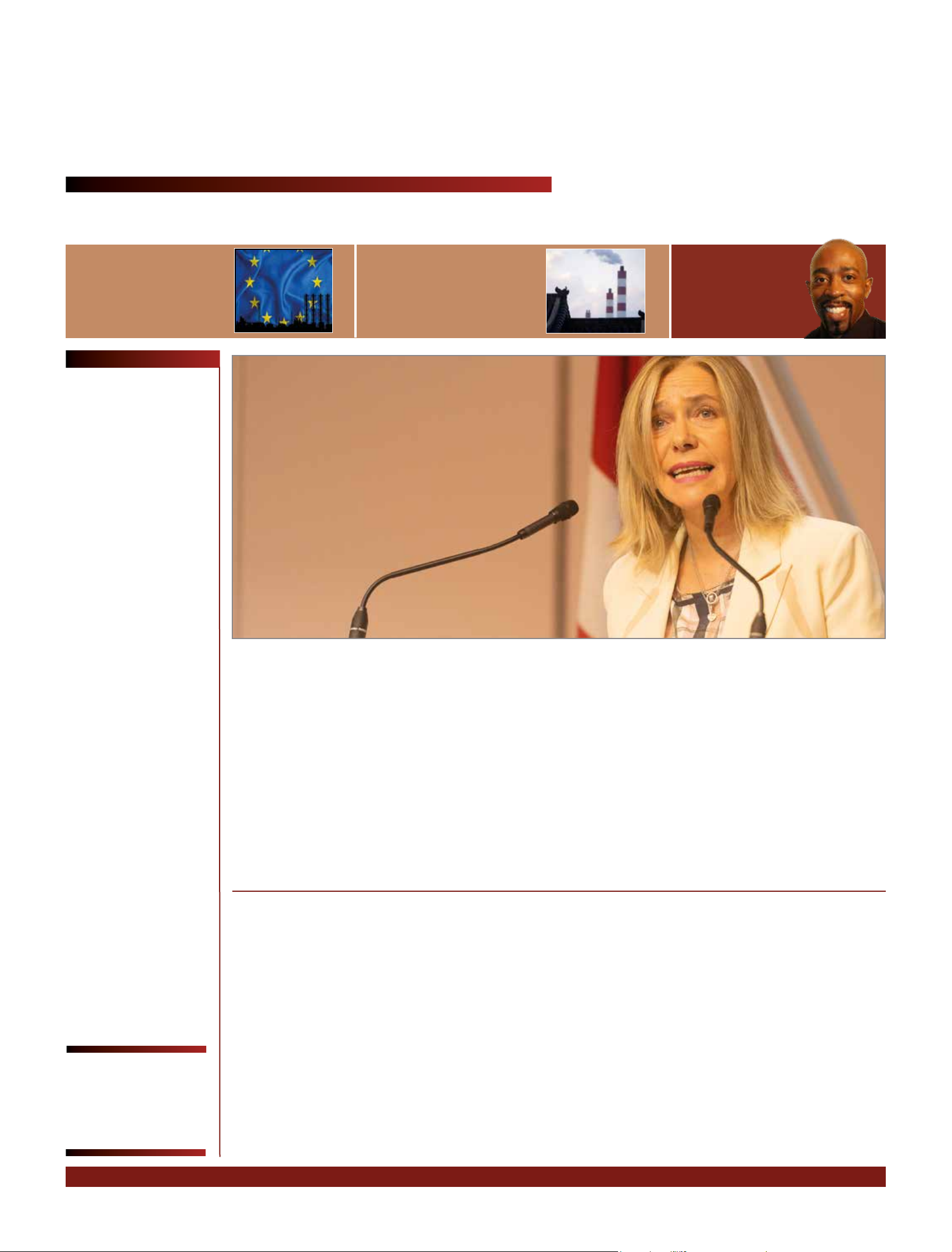
W
hen it comes to cutting car-
bon emissions from steel
production, Italy is argu-
ably already ahead of the game. The
majority (more than 85 per cent) of
its steel is produced from electric arc
furnaces using recycled scrap steel
as feedstock – a much less energy
and carbon intensive method than
blast furnace steel production.
But for one of the country’s major
steel producers, this is not enough.
The ORI Martin Group has complet-
ed the most recent phase of its ongo-
ing effort to reduce emissions while
improving energy efciency across
its plants. The company recently be-
gan operating a large scale heat
pump in Brescia in its latest move to
further improve the plant’s energy
efciency and reduce carbon emis-
sions by a further 5000 t/year.
Brescia, a historic city in the region
of Lombardy between Milan and Ve-
rona, has a long history in demon-
strating its commitment to sustain-
ability and energy efciency. In 1972
it began developing an integrated
system for energy production, dis-
trict heating (DH) and heat recovery
from industries. Over the years the
expansion of the DH network, the
introduction of cogeneration plants
and waste to-energy technology has
seen the city gain international rec-
ognition as a good example of circu-
larity and efciency.
More recently, recognising the
need to play its part in tackling cli-
mate change, in 2021 Brescia issued
the City Charter for Climate Neu-
trality. It has set a target of reducing
per capita CO
2
emissions by 50 per
cent by 2030 compared to 2010. The
target does not take into account
emissions from the private produc-
tion, or industrial sector.
Yet industry has a big part to play.
Over the last decade or so, ORI Mar-
tin has been accelerating its activities
in support of the city’s sustainable
development and climate-neutral
ambition.
“The steel industry is one of the
biggest industrial emitters of CO
2
emissions. It accounts for more than
7 per cent of the world’s CO
2
emis-
sions. We have to decarbonise to be
in line with the EU’s pledge to de-
crease emissions by at least 55 per
cent by 2030, compared to 1990 lev-
els… ,” said Carolina De Miranda,
Sustainability Manager, ORI Martin
S.p.A. “This year we started our de-
carbonisation strategy to reduce our
Scope 1 and Scope 2 emissions by
30 per cent by 2030, compared to
2018. And we would like to use up
to 25 per cent renewable energy in
our process.”
Commenting on the Brescia site
specically, she added: “We are lo-
cated next to a residential area,
which has always pushed us to work
on sustainability. So we started to
work on sustainability a long time
ago, especially for this location. ”
The Brescia site has been a key
focus for the company. In 2016 it
began working with Turboden, a
Mitsubishi Heavy Industries com-
pany, to see how the steel plant
could contribute to the city’s drive
to improve energy efciency. It in-
vested €12 million in a project
called ‘I-Recovery’ to convey the
large amount of heat contained in
the fumes of the electric arc furnace
into a system to avoid it being wast-
ed to the atmosphere.
The heat is recovered by a waste
heat recovery steam generator that
generates steam, which is then used
to feed the district heating network
in winter, or converted into electrici-
ty in the summer months through a
2.5 MW Turboden turbine using an
Organic Rankine Cycle (ORC). Both
the heat and electricity are supplied
to local energy company A2A to
serve its customers. The system has
an annual heat recovery capacity of
52 GWh and has reduced CO
2
emis-
sions by 10 000 t/year.
In its ongoing mission to cut car-
bon emissions and improve energy
efciency still further, ORI Martin
again turned to Turboden to recover
even more heat from the process. A
project known as ‘Heat Leap’ was
launched in 2020 as part of the ‘Life’
programme funded by the EU. Oper-
ation of this €6.5 million project
started earlier this year.
Roberto de Miranda, Board Mem-
ber, ORI Martin, said: “We use a lot
of water in the process for cooling.
Normally we use a cooling tower to
cool down the water used to cool the
electrical furnace. Now we can send
the water to a large heat pump (LHP)
to recover even more heat.”
Thanks to the installation of the
LHP, the heat from the furnace
cooling water can be upgraded and
then re-utilised instead of being
wasted, i.e. dissipated through cool-
ing towers.
For this project, Turboden designed
and installed an innovative LHP sys-
tem. With a Coefcient-of-Perfor-
mance (COP) of 8.2, it elevates the
waste heat (using electrical energy)
coming from the low-temperature
thermal waste heat of the steel plant,
from about 70°C up to as much as
120°C, to transfer it to the local dis-
trict heating network. Turboden’s
LHP has a thermal output of up to 7
MWth and is capable of adapting its
operation to specic process condi-
tions, thereby maximising energy re-
covery from the steel plant.
It will also be able to regulate the
heat transfer temperature according
to the specic needs of the district
heating network, up to a maximum
of 120°C. According to the compa-
ny, this is an important innovation
compared to the maximum tempera-
tures achievable by conventional
heat pump technology.
It was a complex project. The over-
all architecture of the installation
was carefully studied before pro-
ceeding to any real work on site.
Overall installation drawings were
done, as well as detailed engineering
and computer-assisted design, espe-
cially on the different interfaces be-
tween sub-systems. Firstly, the LHP
was connected to the existing waste
heat recovery (WHR) system and
designed in such a way that it can
accommodate variations of the heat
source temperature, thus providing
constant temperature to the WHR in-
stalled downstream.
The LHP was assembled on site,
accounting for local constraints and
nal ne-tuning of connecting pipes.
The LHP was then thermally insulat-
ed to avoid heat losses, as well as to
ensure safe access for authorised
maintenance staff.
The LHP was installed sufciently
close to the WHR system to mini-
mise temperature drops, and all con-
necting pipes were thermally insu-
lated. Assembly was carried out
on-site. In addition to mechanical
and hydraulic works, the LHP in-
stallation included electrical works.
The heat pump at the steel works
can be split into its main different
components: a low-pressure com-
pressor skid, where the inlet pressure
is between 4 and 7 bar; a high-pres-
sure compressor skid, where the out-
let pressure is between 7 and 10 bar;
a condenser; and an evaporator.
Roberto Bertanzi, Product Devel-
opment Coordinator at Turboden
said: “The water needed to cool the
furnace used to be wasted but thanks
to the heat pump, it can be now heat-
ed from about 70°C to around 100°C
for feeding into the district heating
system. It works in parallel with the
system that recovers heat from the
furnace fumes.” He added: “It’s
quite a exible system; we use soft-
ware to optimise heat production in
summer and winter. This is a pio-
neering project.”
Bertanzi noted the growing use of
heat pumps throughout various in-
dustries due to their ability to pro-
vide both heating and cooling as
well as the pressing need for decar-
bonisation. “They are, for example,
needed in the food industry and dair-
ies,” he said. “They are also well
suited for carbon capture processes,
which need both heating and cooling
for the chemical processes used to
remove CO
2
.”
He concluded: “The heat pump
helps support decarbonisation of
heat. So every time you are produc-
ing heat, you have to ask: ‘Can I re-
cover heat somewhere else by us-
ing a heat pump to reach my target
temperature?’ It’s not just about
saving money; it’s about saving the
environment.”
ORI Martin’s steel
production plant in
Brescia, Italy, is a
good example of how
the sector can play its
part in cutting global
carbon emissions.
Junior Isles recently
visited the facility to
take a look.
Brescia steel factory pioneers
Brescia steel factory pioneers
decarbonisation technology
decarbonisation technology
THE ENERGY INDUSTRY TIMES - APRIL 2024
15
Technology Focus
Maximising heat recovery at
the ORI Martin steelworks in
Brescia, Italy
Photo courtesy: ORI Martin