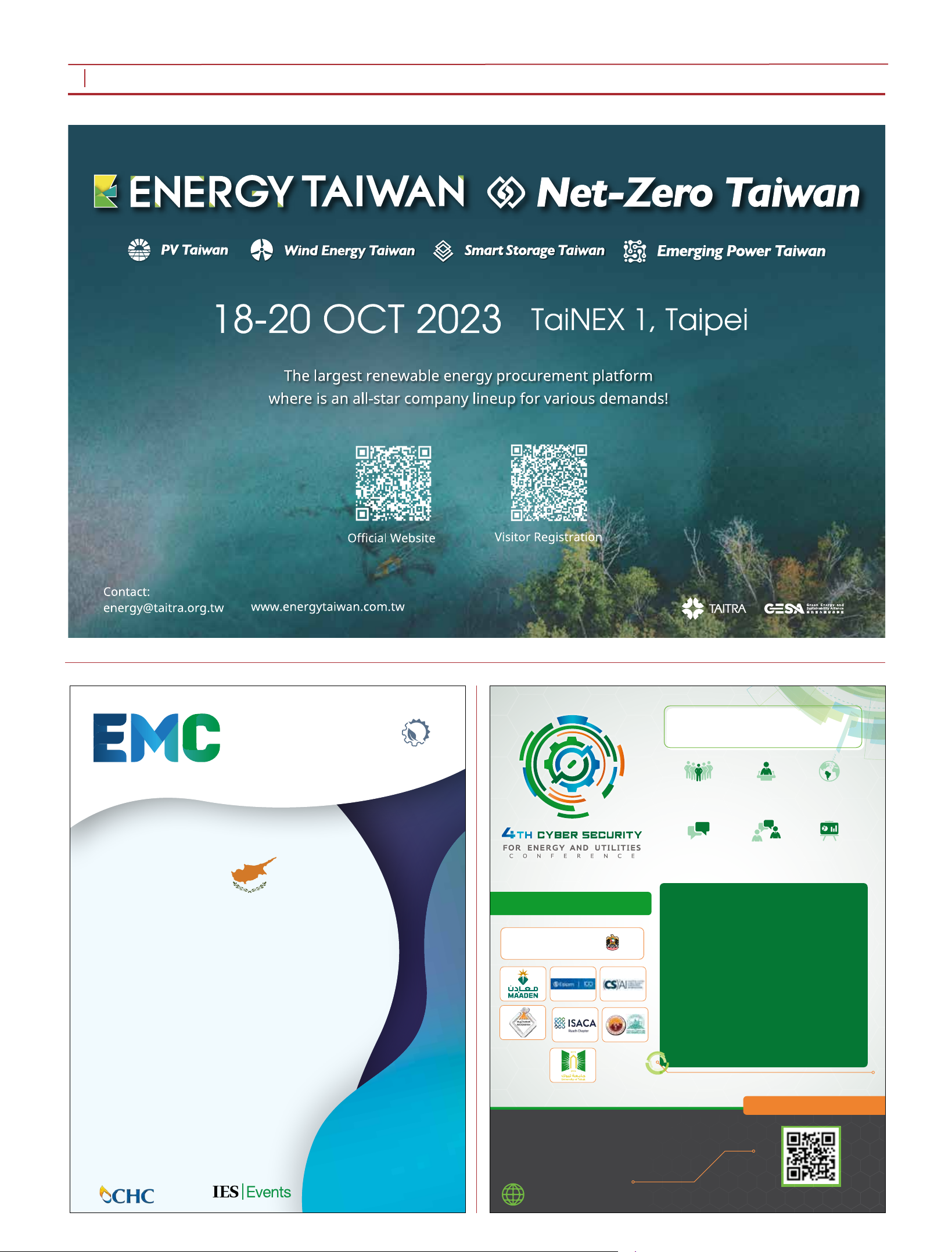
THE ENERGY INDUSTRY TIMES - SEPTEMBER 2023
Special Technology Supplement
F-gas-free switchgear at the
Siemens Energy switchgear
factory in Berlin
allows more efcient compression,
further reducing the energy con-
sumption of the plant (and resultant
CO
2
footprint).
“This lies at the heart of what we do
at Siemens Energy. We have a busi-
ness area that specically looks at
how we reduce the carbon footprint
of industrial processes; steel is one of
them,” said Sengupta.
Siemens Energy is building on its
Salzgitter compressor experience, with
plans to install an advanced rotor hy-
drogen compressor at another steel
production plant in Sweden. It will
meet the steel producer’s requirement
for a compressor with higher ow
rates.
“This will be phenomenal because
you won’t need to have multiple
compressors running in parallel; you
can have one large centrifugal com-
pressor, providing all the pressure
ratio and the ow rate at the same
time,” said Sengupta.
“It’s something we are very excited
about and are talking to multiple cus-
tomers about it. The future of green
steel will need a portfolio where we
are not looking at small multiple units
but reliable larger units.”
The use of fewer units, he says will
mean lower costs, higher reliability
and reduced footprint. “Each com-
pressor has its own balance-of-plant,
so each time you add one more
compressor, the average cost per
megawatt goes up.
“Also steel producers are convert-
ing in a browneld situation, so there
is a space constraint. If you have a
large ow there will at some point
not be enough room for multiple
compressors; so a larger single
compressor with a 1+1 conguration
would be a huge advantage.”
In addition to compressors, Siemens
Energy has also secured a contract to
build a substation on Salzgitter AG’s
premises to connect to the 380 kV
‘Salzgitter Industrial Line’.
The scope of the contract covers a
380 kV gas-insulated switchgear
(GIS); a 220 kV GIS; substation
auxiliary systems; and the entire de-
sign engineering. In addition, Sie-
mens Energy will provide four high
voltage and medium voltage trans-
formers for the rst step of SALCOS.
The substation will be connected via
the Bleckenstedt Süd substation of
TenneT TSO GmbH to the future 380
kV industrial line that in turn will
connect up Salzgitter with the Wahle-
Mecklar line. Going forward, this
grid connection will allow Salzgitter
AG to source the necessary volumes
of power from renewable energies.
GIS is in fact another area in which
Siemens Energy is already contribut-
ing to tackling climate change. The
company has launched a range of
GIS that has eliminated the use of
sulphur hexauoride (SF
6
) – a gas
which is used for insulation with a
global warming potential 24 300
times that of CO
2
.
Siemens Energy has been working
on its ‘Blue’ technology for more
than 12 years, initially focusing on
lower high-voltage levels, i.e. 72.5
kV. The technology is available for
GIS, circuit breakers and instrument
transformers all with absolutely zero
CO
2
equivalent emissions over the
lifetime of the equipment. The tech-
nology has been in service around
the globe up to 145 kV for several
years and is currently being rolled
out across Siemens Energy’s entire
HV switching equipment portfolio
up to the highest transmission level
of 420 kV.
The company also emphasised that
several hundreds of switchgears with
Blue technology are already being
installed in wind turbines. Big off-
shore wind farms currently use 72.5
kV, so it developed switchgear espe-
cially for wind turbine applications
and rst installation started in 2017.
Wind power is one of the corner-
stones of the green energy transition.
With more than 600 GW of new ca-
pacity to be installed worldwide in
the next ve years, it is important for
the wind industry to reduce its car-
bon footprint through developments
such as GIS without SF
6
or other F-
gases. The work Siemens Energy is
doing with Salzgitter also feeds back
into this.
In April this year, Siemens Gamesa
announced the GreenerTower, a
wind turbine tower made of more
sustainable steel.
Towers consist of approximately
80 per cent steel plates. The new
GreenerTower will ensure a CO
2
re-
duction of at least 63 per cent in the
tower steel plates compared to con-
ventional steel. Siemens Gamesa’s
new thorough qualication process
will verify that only a maximum of
0.7 t of CO
2
-equivalent emissions
are permitted per tonne of steel,
while maintaining the same steel
properties and quality.
Salzgitter AG, with its heavy plate
mill Ilsenburger Grobblech GmbH,
is the rst supplier to be qualied,
something, which has also been rein-
forced by third-party certication.
Today, tower production accounts
for more than one-third of all wind-
turbine-related CO
2
emissions. If all
towers installed by the company in
one year were exchanged with
GreenerTowers, it would be the same
as removing more than 466 000 cars
from the roads in Europe for a year.
This new CO
2
-reduced tower will be
available as an option for both on-
shore and offshore wind turbines for
projects to be installed from 2024
onward.
The GreenerTower has already
closed its rst order. RWE and Sie-
mens Gamesa have agreed to intro-
duce 36 GreenerTowers at the 1000
MW Thor offshore wind power
project in Denmark. In total, 72 SG
14-236 DD offshore wind turbines
are planned to be installed starting in
2026. Sven Utermöhlen, CEO RWE
Offshore Wind, said: “Offshore wind
already has one of the lowest life-
cycle carbon footprints of power
generation technologies. At RWE we
are fully committed to working to-
wards circularity and net zero emis-
sions. We are already testing the
world’s rst recyclable wind turbine
blades by Siemens Gamesa under
real-life conditions.”
By piloting the GreenerTower at
our Thor offshore wind farm, RWE
is now looking to take the lead in
helping to signicantly reduce the
carbon footprint of wind turbines.
On average, 1.91 t of CO
2
is emit-
ted during the manufacturing process
for every tonne of steel. By setting a
threshold of 0.7 t CO
2
-equivalent
emissions per tonne of steel, Siemens
Gamesa says it “signicantly” re-
duces the footprint of the largest
component in terms of CO
2
-equiva-
lent emissions.
The use of green steel in its wind
towers goes a long way to closing the
loop in making its wind turbines
completely green.
It certainly feeds into Siemens En-
ergy’s strategy of cutting emissions
from its own operations. “Again, this
is at the heart of what we’re doing at
Siemens Energy and the goals that
we’ve set for ourselves. We look at
Scope 1, Scope 2 and Scope 3 emis-
sions. Every time we supply to the
steel industry, if it’s not green steel it
adds to our Scope 3 emissions,” said
Sengupta. “So we are very actively
engaged to reduce Scope 3 emis-
sions, which means we are actively
engaged to pursue the HDRI. So it
not only helps our customers, it helps
us as well. Ten years down the line,
this needs to be more the norm rather
than the exception.”
He concluded: “Technology is im-
portant but perhaps even more im-
portant is the relationship with our
customers. We have been working
with Salzgitter to build the solution
together, supporting them for the last
5-10 years. It’s partnerships that
make all of this come to life.”
most cases, the operators would like
to switch over from existing natural
gas to a mix of hydrogen before
completely turning over to hydrogen.
The exibility of not having to
change the compression system is a
huge advantage on continued pro-
duction and costs.”
Apart from hydrogen, compressors
are also used in steel plants to handle
nitrogen and oxygen.
Sengupta commented: “There are
compressors that handle dry oxygen
and these are different from the ones
that handle hydrogen and natural
gas, and different from compressors
that handle nitrogen.”
For nitrogen compressors, Siemens
Energy has extensive experience in
the air separation market. These, says
Sengupta, are fairly standard technol-
ogy but need to be extremely reliable.
The oxygen compressors are more
complicated: you don’t want any
ammable material inside. And this is
where we have the experience, with
years of reliable operation; very few
manufacturers can do it. For the natu-
ral gas/hydrogen compressors, this is
where we also have the experience
depending on the size.”
Siemens Energy has secured the
contract to deliver and install its ad-
vanced centrifugal compressors for
compressing hydrogen at Salzgitter,
with an integrally-geared compres-
sor design driving two compression
stages to achieve the required pres-
sure ratio. This portfolio of geared
compressors driving up to four shafts
at individually optimised speeds
The new GreenerTower will ensure a CO
2
reduction of at least 63 per cent in the tower steel plates compared to conventional steel